ALL YOU NEED
Technologies and know-how
For the entire life cycle of your product
What defines the best process for your product, be it in pharmaceuticals, medical technology, or consumer goods? It combines everything necessary. One part consists of sophisticated machine platforms for every development stage. Another is a broad foundation of key processes and technologies developed in-house, such as dosing and filling, assembly, or web processing. We design these processes to be adaptable to new requirements – for example, for new variants or integrating secondary and final packaging. We also consider your market success as early as the lab phase, ensuring that your best process can be scaled reliably throughout the lifecycle of your product.
What we also consider: the aspect of sustainability. Your machine solution from Harro Höfliger is designed for both high efficiency and long service life. Both can be further enhanced through our Customer Services team, such as maintenance, repairs and upgrades, or retrofitting of your next-generation products.
Key processes for your products
Complete competence
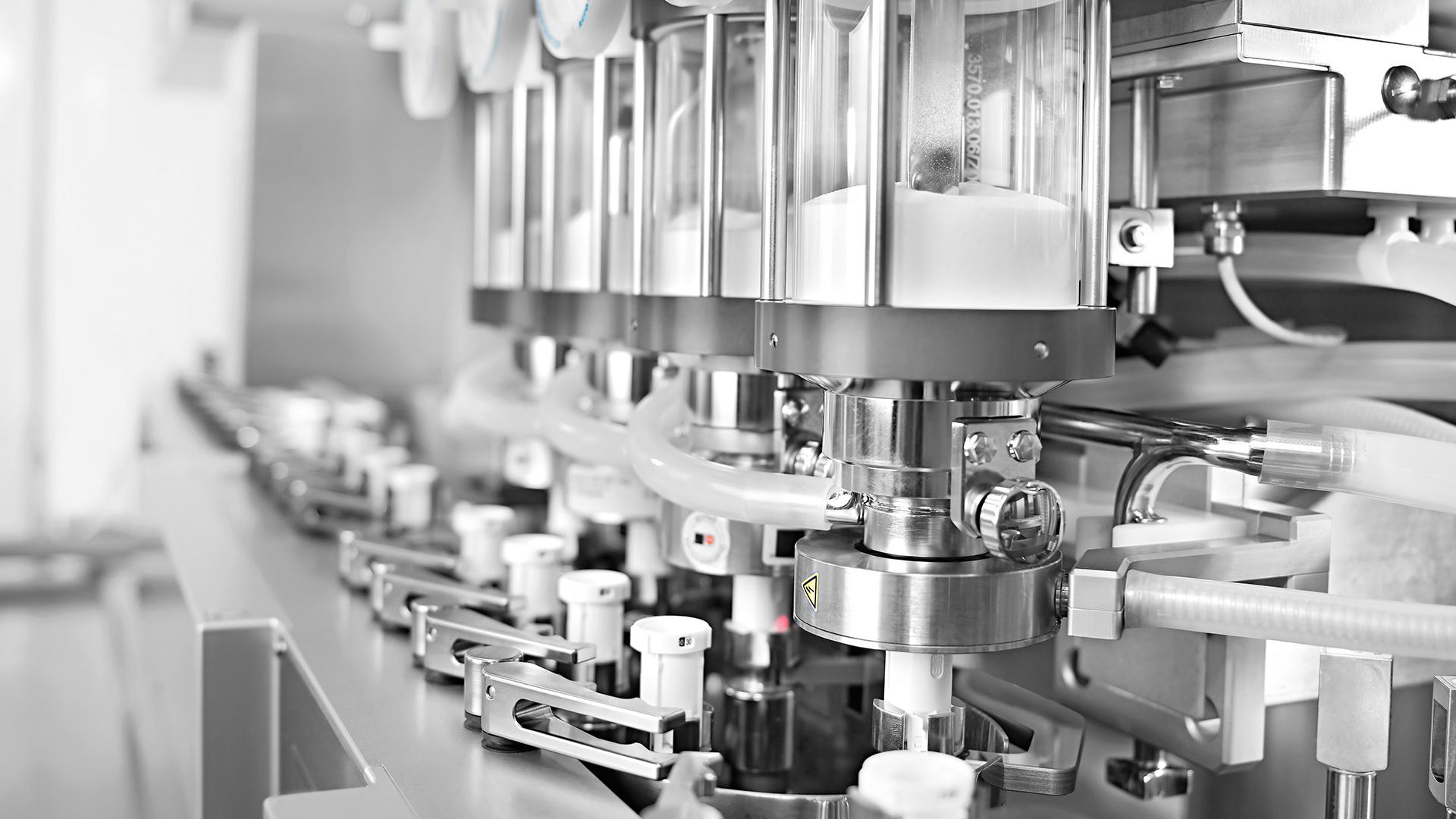
For pharmaceuticals
Dosing and filling, web processing, barrier technology: Just some of the core technologies we have perfected over decades. And with our pharmaceutical expertise, we combine them into your perfectly aligned system solution. Which is far more than just high-tech mechanical engineering.
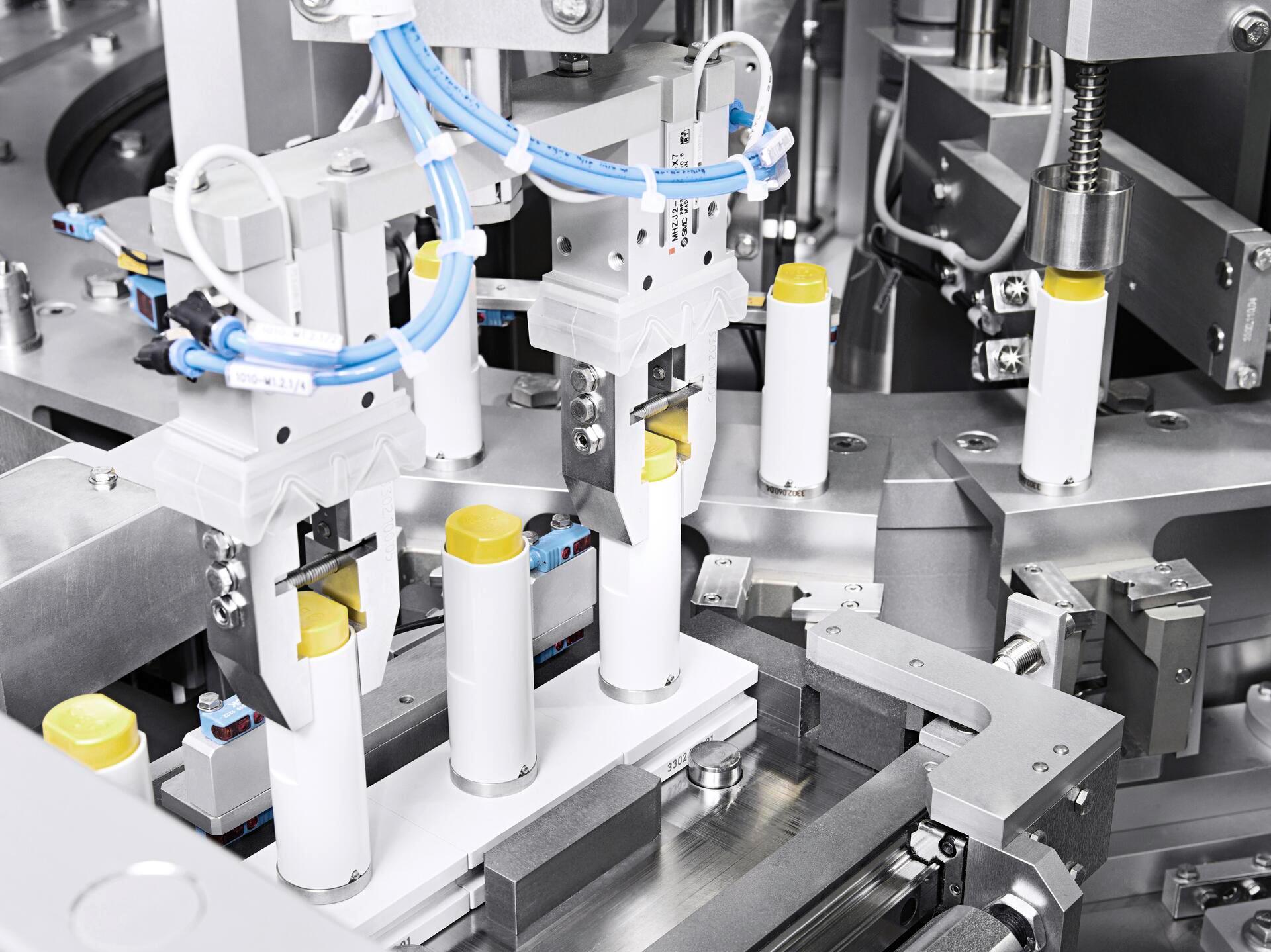
For medical technology
Your success principle for a dynamic market with short innovation cycles: the modular design of our systems. For future-proof processes that keep up with your pace. And despite all flexibility, the highest quality is always ensured in line with regulatory requirements.
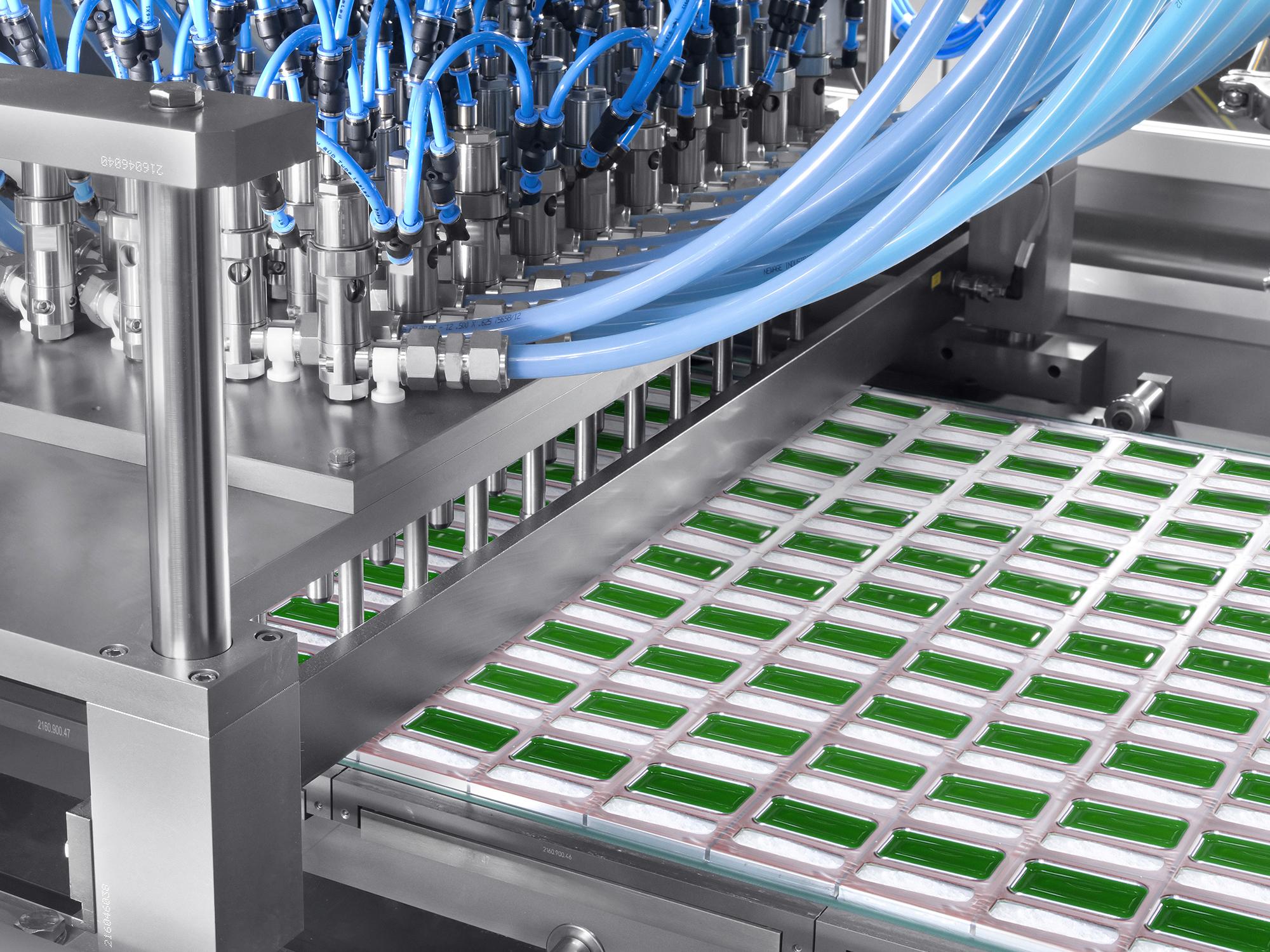
For consumer goods
Portion packs are simply practical, but their manufacturing process is complex. For perfection in all shapes and formats, we combine the right technologies with plenty of know-how. For filling materials and films, sealing methods, and solutions for improved sustainability.
Trade shows and events
Upcoming events
PHI SEA 2025
Kuala Lumpur, Malaysia
Medical Technology 2025
Galway, Ireland