Services
Device Services
Accelerate systematically to market maturity
Whether pharmaceutical devices such as diagnostic test substrates and inhalers, or medical devices like autoinjectors and prefilled syringes: The comprehensive technical problem-solving competence of our Device Services team gets your product ready for production faster. The experts proceed systematically here. They firstly analyze whether and how your product can be realized and produced, and then develop it further hand-in-hand with you. One focus is on minimizing risks in design, product, and processes, with a view to successful scaling up to commercial production. Is your product ready for production and safe for use? We demonstrate this point-by-point with functionality and stability tests.
Device Services is also the right contact for the approval process. The team is very familiar with the MDR regulations for medical devices and the IVDR (In Vitro Diagnostic Regulation). It advises on conformity assessment procedures and prepares all necessary documentation for successful product approval.
Success factors for your pharmaceutical and medical devices
Your expert for Device Services
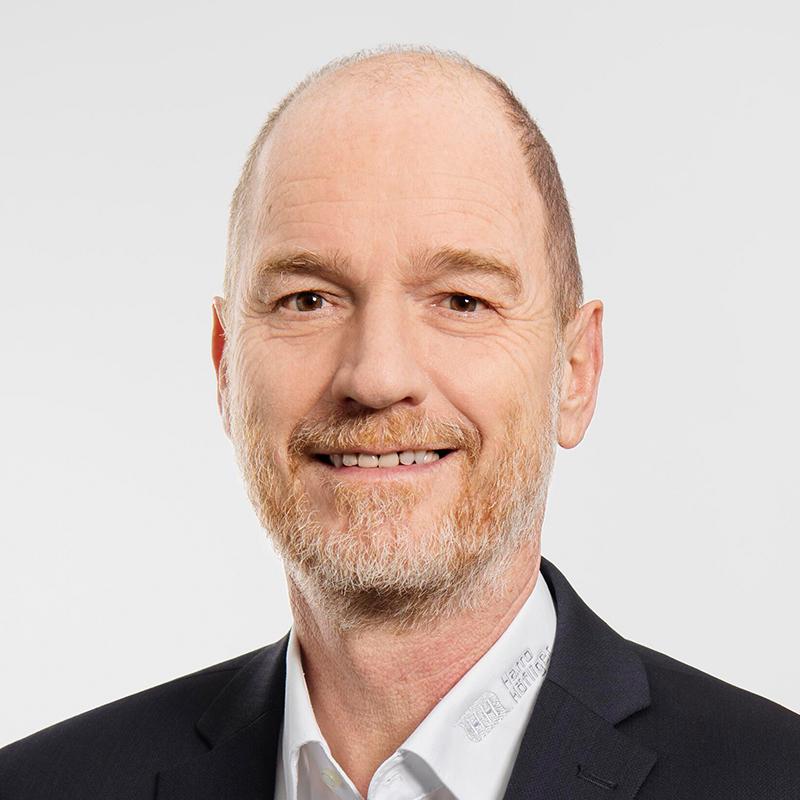
Martin Lober
Team Leader Device Services
From product idea to production
Further services
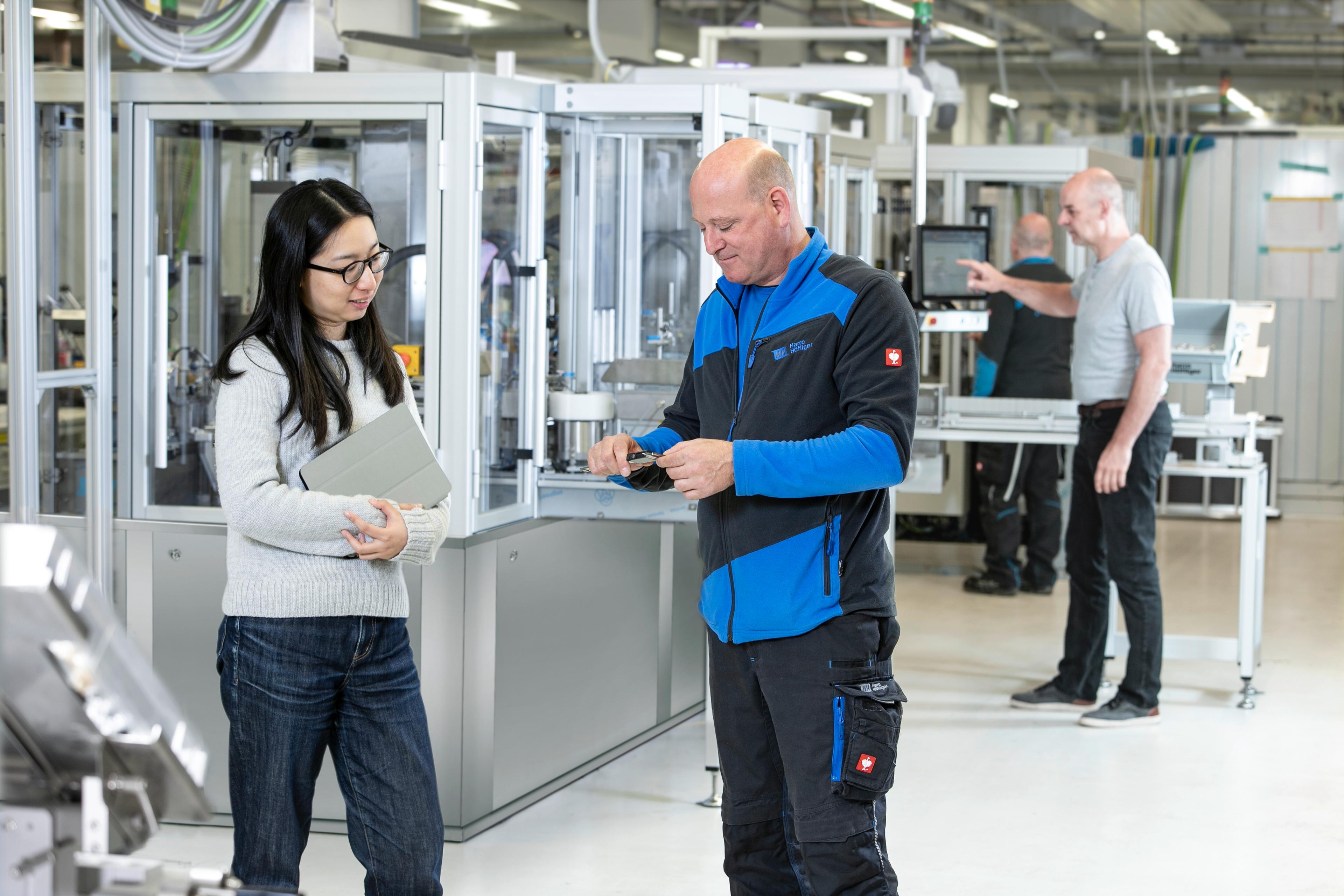
Customer Service
The reliable operation of your process solution and consistently high machine availability over the entire service life: Our global service team provides worldwide support. From rapid support to making production even more efficient.
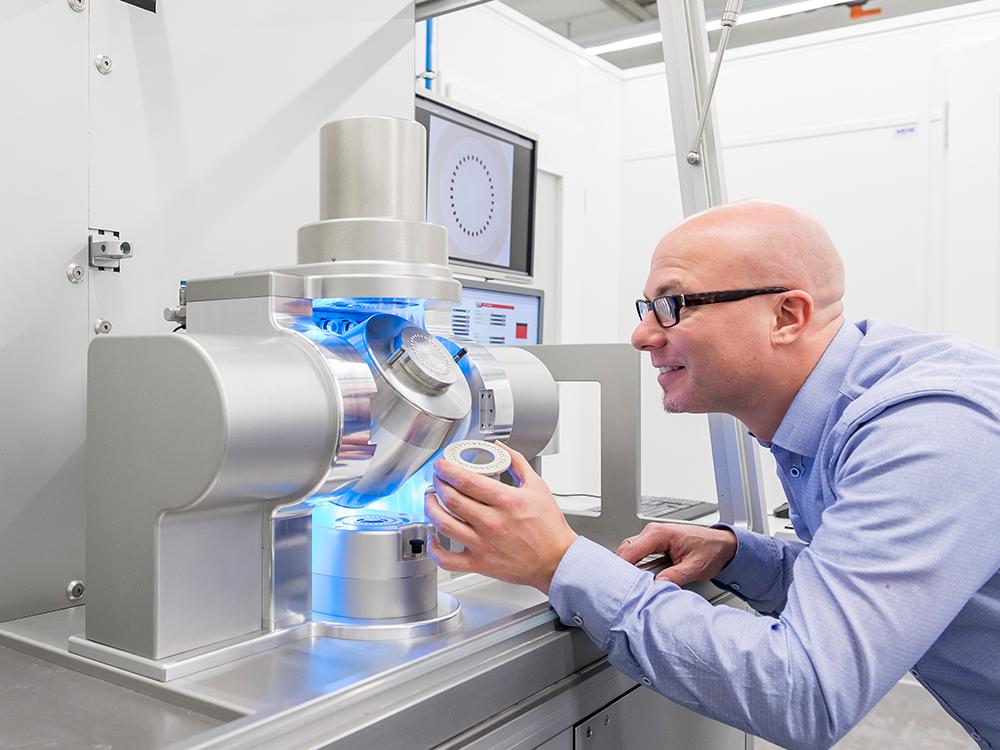
Engineering & Innovation Services
A competitive product requires not only your idea, but also new processes and methods. Developed with know-how from various fields, optimized for seamless transition to the next production stage of your innovation.
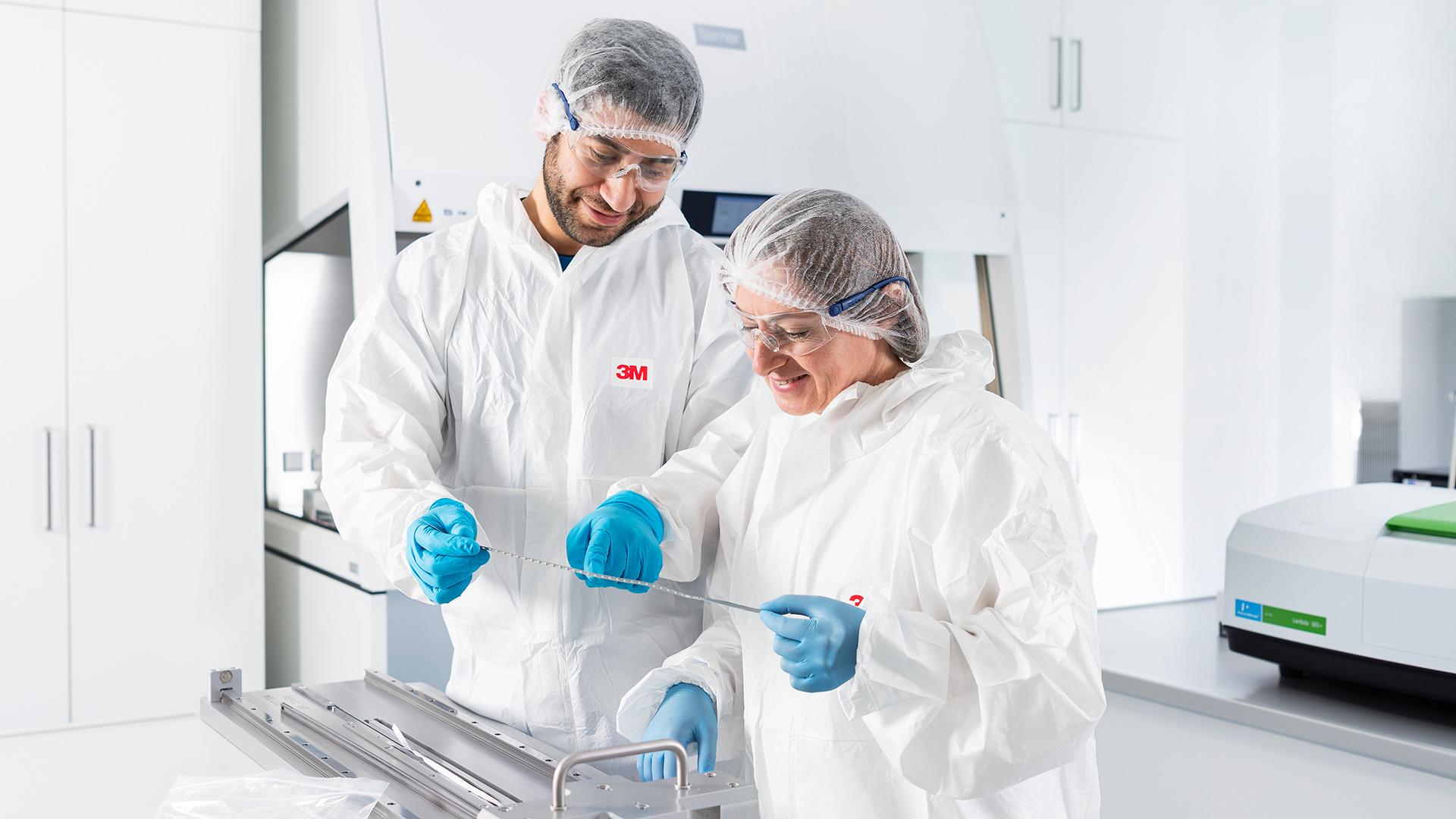
Pharma Services
When and how does process reliability emerge for your new formulations and innovative devices? The earlier, the better. With combined expertise from research, development, and mechanical engineering for efficient, risk-minimized process development.