Customer Service
Maintenance
Ensuring long-term high machine availability
Proactive and plannable inspection, maintenance, and servicing are key elements for your fault-free production. Our preventive services reduce your unplanned downtimes and ensure long-term high machine availability, which can be strategically optimized based on the actual state determined.
Inspection
Maintenance
Servicing
Extending the warranty
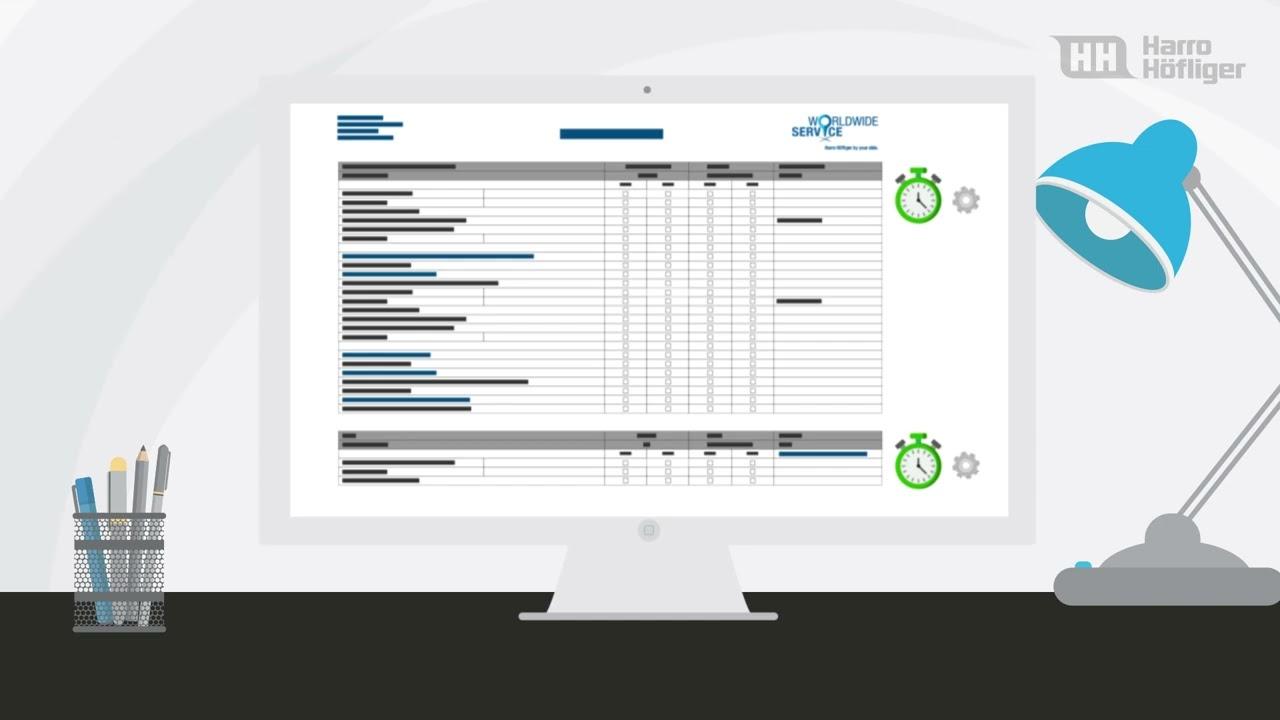
Servicing management
How can you extend the service life of your system and maintain a consistently high level of productivity? With a precisely aligned servicing concept in which all required servicing activities are planned according to your production calendar and are consistently documented after implementation. Firstly, we conduct on-site inspection and assess the actual state. On this basis, we create a package with all the necessary actions to strategically counteract wear on components and the machine.
Identifying and resolving wear
Planning maintenance intervals and budgets
Extending the machine lifecycle
Individually optimizing
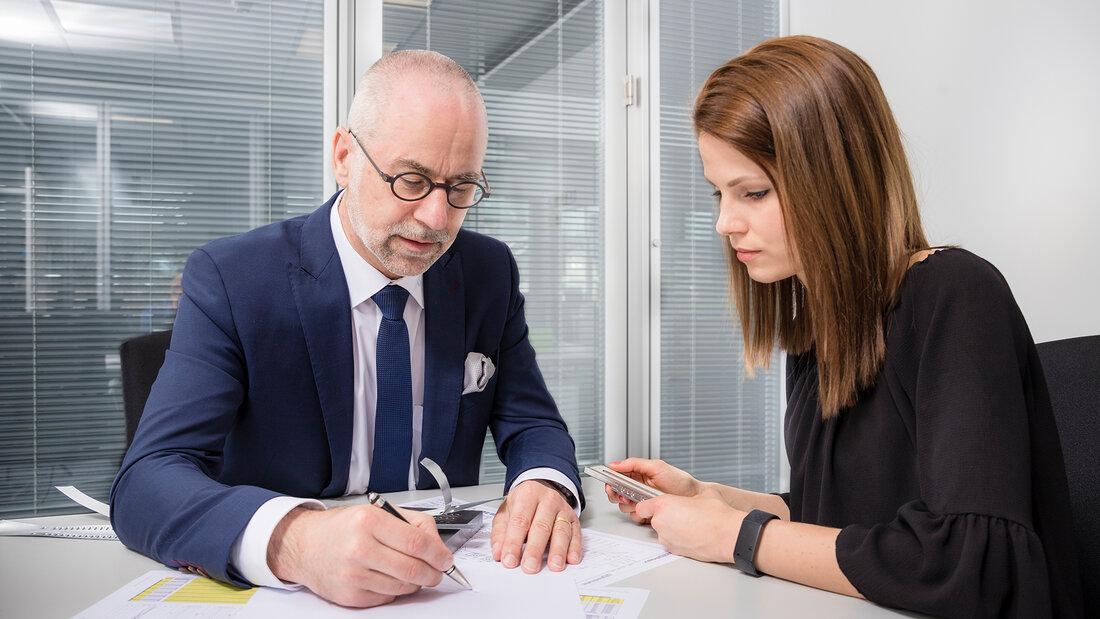
Extending the warranty
Do you always want to be in a position to maintain production as planned? Then a combination of documented maintenance and a warranty extended beyond the statutory 12 months is recommended. The warranty starts from the beginning of production or, at the latest, after the successful site acceptance test (SAT). The extended warranty covers up to 24 months or 6,000 operating hours, whichever comes first.
Making costs predictable thanks to a one-time payment
Preserving the value of your machines and systems
Servicing with manufacturer competence